Replace/Repair Headliner
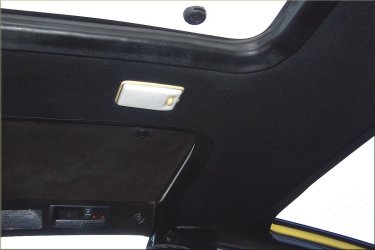
On my 86 Turbo, which already had a pretty nice interior,
one typical problem existed. I didn't even notice or check the headliner
while purchasing (not that it would've made a difference). I noticed it
first when I was going around with protectant wipes getting all the
plastic cleaned up. Well - typical sagging had occurred somewhere in
it's life. Someone tried once or twice to get it stuck back up there,
but when the foam backing is basically powder, it doesn't stick well.
I read the Z31
article about removing the headliner, and AZ-ZBum's
writeup about replacement and I went to town. Removal of the
headliner is a cinch and takes maybe 10 minutes tops. The most difficult
part was removing the rear trim piece, which isn't saying much because
that wasn't too tough, either.
Cost of Repair: $15 for Headliner Fabric and $15 for 3M
Spray Adhesive (I've seen it cheaper online)
The surface of the original headliner was still in pretty
good shape. However, certain sections had warped and the foam backing
was pretty much destroyed around the back edge because of heat, age, and
multiple applications of glue. Some glues will dissolve foam and most
glues will not adhere an old Z headliner to the hardboard backing. The
original headliner has a velvet-like surface which is bonded to what
appears to be a plastic liner, all with a foam backing. Once the foam is
gone, the plastic is all the glue has to stick to, and the padding is
obviously gone, which would case a gap between the trim and headliner
surface. So, basically, the best thing you can do it replace the
headliner instead of trying to get it to stick back on...even if you did
a good job, you'll likely have some warped sections and end up with a
sagging headliner again in the near future.
I removed the metal clips from the holes --- this was a
bit of a pain. Obviously be careful not to bend the hard board because
it will crack or break off. You want these metal clips put back on after
you adhere the new fabric. One of them accepts the clips from the
map-lights so you won't wear into the hardboard by clipping the metal
clips into the hardboard opening.
Worse than anything was the ATTEMPTS previous owners took
on rehanging the original liner. They got glue everywhere. I had to
refinish the hatch trim piece because the glue would not come off
without stripping paint. I stripped it clean and repainted it with black
trim paint from Checker. Looks great : ) Back to the main subject,
however --- many small sections of headliner did not rip off with the
rest of the headliner. It was glued on tight. There were several
sections on the board that had thick, heavy glue. I had to take a razor
blade scraper and carefully get the bulk of it off. Be careful if you
have to do this because the blade will easily start to cut into the
hardboard. It took me about 90 minutes to clean off the bulk of the
glue. Then I used an orbital sander to even things out as good as I
could without ruining the shape or thinning out the board too much. I
used some citrus cleaner on some of the sticky glue residue that was
left over. There as both sticky, wet glue residue and hard stuck on
glue.
As described in the write-ups, any normal sections with
stuck on old foam were easy to work with. Just rub it off with a medium
coarse scotch-pad. I tried to remove any "high" areas where glue was a
bit thicker. When done, the majority of the surface had a uniform rough
look (except for the part I had to sand). I took 200 grit wet sand paper
(used it dry) and just went over the entire surface lightly to clean it
off and get a good bonding pattern for the new glue.
I went to Jo-Anns Fabric and bought the black, foam-backed
headliner. Hopefully the foam used now is a bit more resilient that the
foam backing used on the original headliner. There is not a plastic
liner, at least, so if it ever sags again, reparation might be possible
(thought the gap would still be an issue with repair). Cloth may also
shrink over time (maybe not warp, but shrink).
Although both the write-ups above are great, I followed
this one a bit more closely:
HEAD LINER
REPAIR
I did not want to use staples, and I figured a
well-adhered headliner is not going to need staples to keep it up. I
found several spray adhesives at Checker, AutoZone, and HomeDepot.
However, none of them were high-heat resistant. Basically all of them
said they were for automotive fabric and carpet, but not to be used for
headliner. Even some that said they were specifically for headliner
basically said not to use them for headliner : ) One 3M can was labeled
as General Purpose Spray Adhesive. It said not to use it for headliner,
but rather to use 3M™ Super Trim Adhesive. I found this stuff at NAPA,
along with several other suitable spray adhesive products (all high heat
resistant). The can said 3M Super Trim Adhesive - 08090 Yellow. Specific
directions are included. I imagine this stuff is really good. However,
it was kind of funny that this can said not to use it on lightweight
foam/fabric...I basically ignored this recommendation because at this
point, it appeared NOTHING was recommended for foam-backed
headliner....one can tells you to use high heat resistant, and the high
heat resistant glue tells you to use general purpose. HA! I tested the
glue on a small section of headliner fabric and it appeared to hold up
just fine to a light coat.
3M™ Super Trim
Adhesive, 08090, Yellow, Net Wt 19 oz/539 g, 6 per case
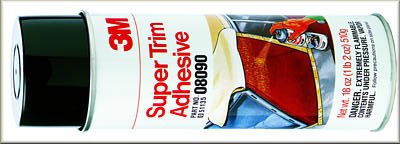
|
Aerosol contact adhesive
designed for bonding vinyl tops, heavyweight liners and hood
silencer pads where high strength and heat resistance are
needed. |
Outstanding features:1.) High immediate bond strength2.)
Re-positionable during assembly3.) Excellent heat and water
resistance4.) Plasticizer resistant5.) Long-bonding range (5 minute to 1
hour)6.) Lace-like, non-misting spray7.) No need to purge after use.
Note: Not recommended for polyethylene, polypropylene or foamed
polystyrene.
I laid the hardboard across the fabric and cut the fabric
about 1 1/2" wider on each edge. The reason I cut out the fabric before
hand was because I wanted to save the large sections that would be left
over without getting glue on it and because I thought it would make it
easier to line up, glue, handle, and pull apart from the cardboard --- I
think all of these turned out to be right. Then I layed a large flat
section of cardboard on the ground (outside, warm day), laid down the
hard board, and then the cut fabric. I folded over half of the fabric,
laid cardboard between it and the other half of fabric (to avoid getting
glue sprayed on the surface of the other side). I put down a light, even
coat of glue on the foam side. Then I sprayed a heavier coat on the hard
board.
The glue sprays out in a criss-cross pattern and gets a
bit stringy, so be careful to do this when there is no wind, and make
sure you don't get any glue on the your nice new fabric surface (either
from your hands or accidentally from overspray).
I let the wet glue sit for just a bit, until it got a bit
tacky (only a few minutes). Then, with a helper, I pulled the fabric
down slowly and put light, even pressure from the center outward, slowly
laying down more until I reached the cross section of the hard board
panel, and then likewise with the close from the center to each end. DO
NOT PULL THE FABRIC so as to stretch it out --- just lay it lightly and
evenly. The stuff is VERY forgiving -- you aren't likely to crease this
stuff -- it was a piece of cake to get it to set down well. Make sure
you apply enough pressure to get it well adhered, but NOT SO MUCH that
you soak up glue into the foam. This can cause several problems --- hard
spots, permanent compression (if the glue dries when the foam is
compressed), and staining of the fabric. The glue WILL BLEED through if
you are not careful. This is why some prefer to use a velvet upholstery
(as well as to get the factory, fuzzy look).
Now that half was done, I let it sit for 30 minutes and
waited to do the next side. Copy the same procedure for the next side.
Let it dry for several hours, if not a day, in 75 degree heat (inside or
warm day).
As I mentioned before, I left generous excess around the
edges. Part of the reason I left excess was so I could decide whether to
fold it back over the board and glue the edges down. I decided to just
cut the edges off because I remember that having it folded over on my
'84 headliner (was redone "professionally") cause a bit of a problem
with setting it back into the front/windshield trim. It becomes thick
and a bit tough to deal with. If you staple it down, that would probably
help since it would be compressed, but still, it's going to be thicker.
Also, the writeup I followed mentioned that if there is trim used around
the edges, you don't need to fold it over (sounds like folding it over
is for aesthetics). I really think the 3M heat resistant glue is strong
enough to hold up this rather light material and I don't think it will
be a problem for a VERY, VERY long time.
So, I gave the edge about 1/4" just for possible
shrinking/pulling/tugging. Then I re-installed the metal clips (big pain
in the butt, again, be careful not to use too much force). The I stuck
the headliner back in the car. I had a bit of trouble lining it all up.
Set it back into the rear, side trim pieces. Then carefully work the
front end into the windshield trim. Then focus on getting the dome light
screw back in it's place. If you can get this screw in, the whole
headliner will be set up nicely for the other screws.
Once I had the four other headliner screws in place, I
worked on some of the accessory items (rear-view, dome light, map
lights, and rear trim. I used a small screwdriver to find where the
screw holes were for things. I waited to attach the visors themselves
until I had the T-Top trim back in place with the front screws set into
the A-Pillars. Then I snapped on the A-Pillar trim and did the visors.
Then I attached the hooks.
It felt good to get this done. It looks very nice, and
total cost (minus opp. cost of my time : ) was $15 for the fabric and
$15 for the glue can. Yep, the glue is a bit pricey.
CLICK ON IMAGES BELOW FOR LARGER FORMAT
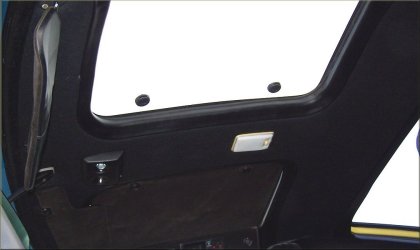
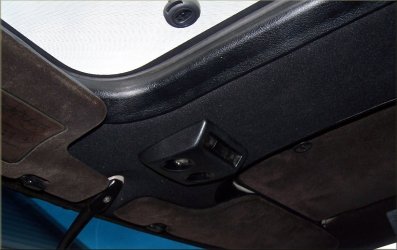